Upskilling Isn't Enough: Mastering Quickskilling for Today's World
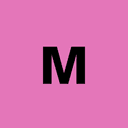
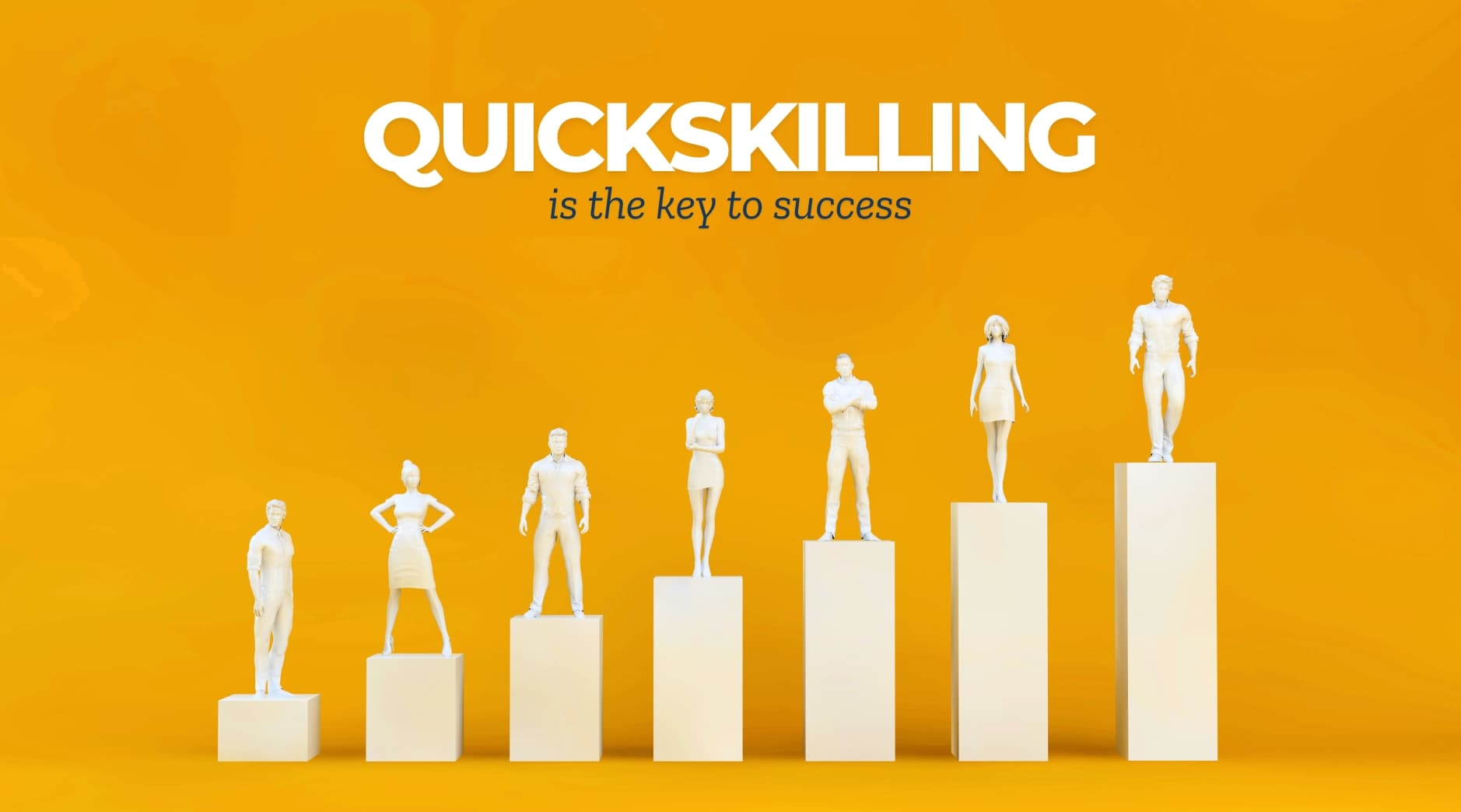
The Growing Challenge of Upskilling in Manufacturing
Upskilling has become a major challenge for manufacturers, driven by a persistent skills gap and the increasing complexity of modern manufacturing technologies. In 2020, manufacturers spent approximately $26.2 billion on internal and external training initiatives to address the shortage of skilled workers.
In 2025, companies continue to make significant investments to bridge this skills gap.
-
Siemens recently announced a $285 million investment in U.S. manufacturing, with plans to open new facilities in California and Texas, creating over 900 skilled jobs (Source).
-
Eli Lilly & Co. is set to invest $27 billion to expand U.S. manufacturing, adding four new sites and generating 13,000 high-wage jobs (Source).
These large-scale investments reflect the industry’s commitment to workforce development, but the rapid pace of technological change means that continuous adaptation and upskilling are necessary to maintain competitiveness in the global market.
The High Attrition Problem & Its Impact on Upskilling
Despite these investments, the inability to attract and retain skilled workers has been the number one concern for manufacturers. One-third of companies have had to turn down business opportunities due to a lack of available talent in the last couple of years.
What is Attrition & Why is it a Problem?
Attrition refers to the rate at which employees leave a company over a specific period. In 2025, employee turnover rates remain alarmingly high:
-
Manufacturing Industry: 37% attrition rate
-
Construction Industry: 54% attrition rate
-
Temporary/Contract Workers: Up to 400% attrition rate
(Source: Award.com)
How High Turnover Affects Workforce Training
-
Increased training costs. Frequent employee turnover leads to higher expenses for onboarding and training replacements.
-
Reduced productivity. New hires require time to ramp up, disrupting workflows and slowing production.
-
Lower morale. High turnover demoralizes existing employees, creating a cycle that’s hard to break.
According to a report by Deloitte and The Manufacturing Institute, the industry will need 3.8 million jobs filled between 2024 and 2033, but nearly half of these roles could remain unfilled due to recruitment and retention challenges (Source).
This trend underscores the urgent need for retention strategies and faster workforce upskilling solutions.
The Root Causes of High Attrition in Manufacturing
A 2025 study by SHRM (Society of Human Resource Management) identifies the key reasons for high attrition among frontline workers and managers:
-
Low wages. Many workers feel underpaid for the level of effort required.
-
Lack of career growth. Minimal opportunities for promotion and skill development.
-
Burnout & work-life balance issues. Long hours, stressful environments, and safety concerns.
-
Toxic work cultures. Poor managerial support and low employee engagement lead to dissatisfaction.
-
Digital job market expansion. New online hiring platforms give employees more job options, making it easier to switch employers.
Especially post-COVID, many workers have started prioritizing well-being and job security, making employers who invest in career growth and employee welfare far more attractive.
The Need for Quickskilling: A Game-Changer for Workforce Development
Manufacturing training times can range from weeks to years before an employee reaches full proficiency. But high turnover rates mean that many workers leave before companies can even benefit from their upskilling.
The solution is to reduce training time without compromising learning quality.
Quickskilling is the rapid training of employees using advanced learning frameworks, immersive simulations, and AI-driven training tools.
Why Quickskilling?
Quickskilling is a game-changing approach that reduces training time while maintaining effectiveness. It enables employees to acquire critical skills faster, allowing them to adapt to technological advancements and operational demands. Beyond new hires, quickskilling helps existing employees stay updated on evolving innovations, making it essential in modern industry.
How Immersive Technologies & AI Can Accelerate Quickskilling
Virtual Training Simulations (VR/AR-based learning)
This creates realistic, interactive simulations where employees can practice machinery operations in a safe, controlled environment. This method enhances comprehension, speeds up skill acquisition, and builds confidence without real-world risks.
AI-Driven Virtual Assistants
This provides an instant feedback and real-time support during training, helping workers understand complex procedures quickly. These intelligent systems can answer questions, offer step-by-step guidance, and extract key information from a company's technical documentation.
Customized Learning Paths (AI-based skill mapping)
CLP uses AI to analyze employee performance and tailor training programs to individual learning needs. Personalized training improves knowledge retention and practical application, ensuring that workers focus on the most relevant skills.
Reduced Downtime & Improved Accuracy
It is another advantage of immersive training. Employees can develop proficiency without disrupting production lines, minimizing costly errors and improving efficiency when transitioning to real-world operations.
Magnimus: Leading the Way in Quickskilling with Immersive Technology
At Magnimus, we specialize in custom VR/AR-based training modules tailored for manufacturing and OEM operations.
Our Quickskilling Solutions Cover:
-
Assembly Line Workers. Hands-on interactive modules for efficient skill-building.
-
Maintenance & Troubleshooting. AI-powered step-by-step guidance.
-
Remote Training. Multi-user VR/MR sessions for collaborative learning.
What Makes Magnimus' Approach Unique?
-
Multi-Platform Integration. We offer VR, Mixed Reality (MR), and Augmented Reality (AR) setups.
-
Detailed 3D Interactables. Workers can explore highly detailed machinery components without physical access.
-
Cloud-Based Training. No need for local installations—ensures high security & scalability.
By reducing training time, improving retention rates, and making learning immersive, Magnimus helps manufacturers bridge the skills gap while cutting training costs and minimizing attrition impact.
Final Thoughts: The Future of Workforce Training
The manufacturing industry cannot afford to rely on traditional training methods anymore. With high attrition rates, rising training costs, and increasing job complexities, Quickskilling through immersive technologies and AI-driven learning is the future of workforce development.
Manufacturers that adopt these cutting-edge training solutions today will stay ahead of the competition, improve employee retention, and ensure a skilled workforce for years to come.
Want to See How Magnimus Can Help Your Workforce?
Contact us for a free demo today.
Key Takeaways
-
Quickskilling reduces training time & costs.
-
VR/AR-based simulations accelerate learning.
-
AI-driven training improves accuracy & adaptability.
-
Magnimus delivers scalable, immersive workforce solutions.
The future of workforce training is here. Are you ready?